LUGE: Horizontal steering wheel system assembly MR350LRS
The LUGE steering wheel system is the most important core hardware subsystem of automatic vehicles, which together with the dispatch management system, computer control system, navigation system, power supply system, functional (such as lifting, flipping, etc.) system, and vehicle body system constitute the seven major subsystems of AGV.
LUGE steering wheel system configuration:
1. Drive wheels, reducer, electromagnetic brake (including manual release), permanent magnet synchronous motor, 5VDC incremental encoder;
2. Steering gear, drive gear, speed measuring gear, reducer, DC brush motor, left and right limit switches and mechanical limit switches, 5VDC incremental encoder with anti-impact vibration or optional multi turn absolute encoder;
3. Drive controller: Maximum rated current 175A, maximum peak current 350A. Analog or CANopen digital;
4. LUGE-SR shunt voltage regulator: In the servo system, when the actuator feedbacks energy during deceleration, the bus voltage rises to the clamp voltage set by the shunt voltage regulator, and the shunt voltage regulator starts working to ensure that the bus voltage does not overvoltage. The shunt circuit can withstand a peak current of 160A;
5. Steering wheel system operation software and secondary development library: DriveWare is a powerful software for communication, configuration, debugging, monitoring, and control of steering wheel systems. The built-in motion control function can achieve trajectory planning and motion optimization of the wheel system, and reduce the burden on the upper controller. Drive Library is an advanced API interface that defines a collection of control functions to support developers of motion control solutions;
6. Preset parameter document: The system configuration, parameter optimization, debugging, and aging of each drive are completed before leaving the factory, ensuring that the entire system can cope with most road conditions without debugging, eliminating the uncertainty brought by on-site debugging. The preset parameters have been stored on the corresponding drive and will be sent to customers and our after-sales service team via email.
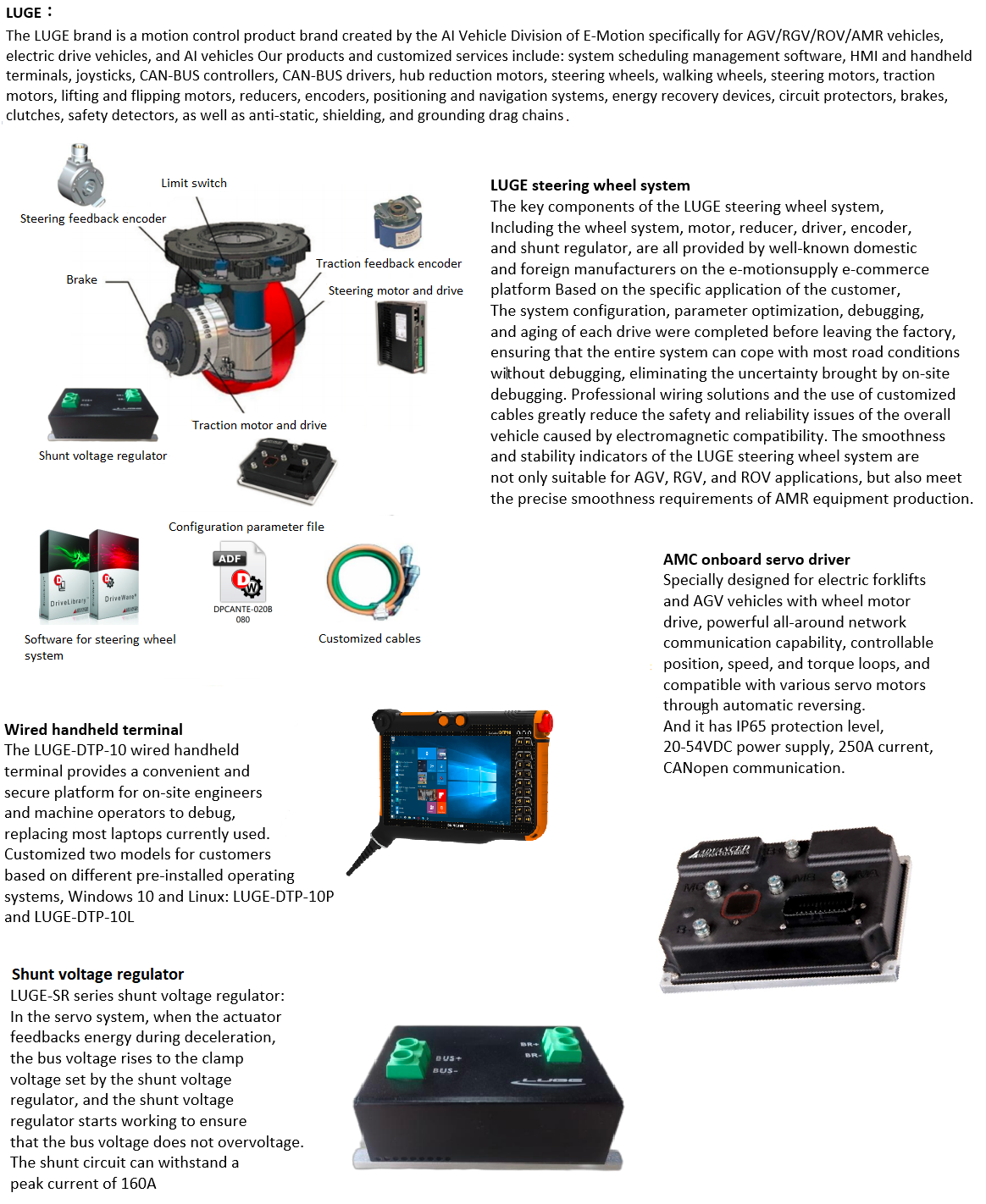
Motor Specifications

LUGE steering wheel system assembly
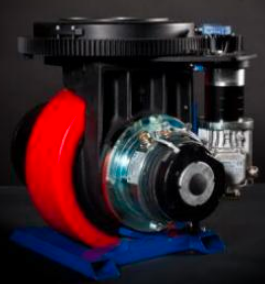
LUGE Steering wheel system MR350LRS - Traction motor drive - DVC250A060
MR350LRS Traction motor adopts high-end imported brand servo drive, AMC servo drive, model DVC250A060
DVC250A060 DC Digital Brushed/Brushless Servo Driver. Powerful all-round network communication capability, position, speed and torque ring are all controllable, and it is compatible with various servo motors through automatic commutation. With built-in I/O and control programming capabilities, a single or multiple controllers can be used to realize various tasks of logic control and motion control in any combination of single or multiple units.
Model Parameters
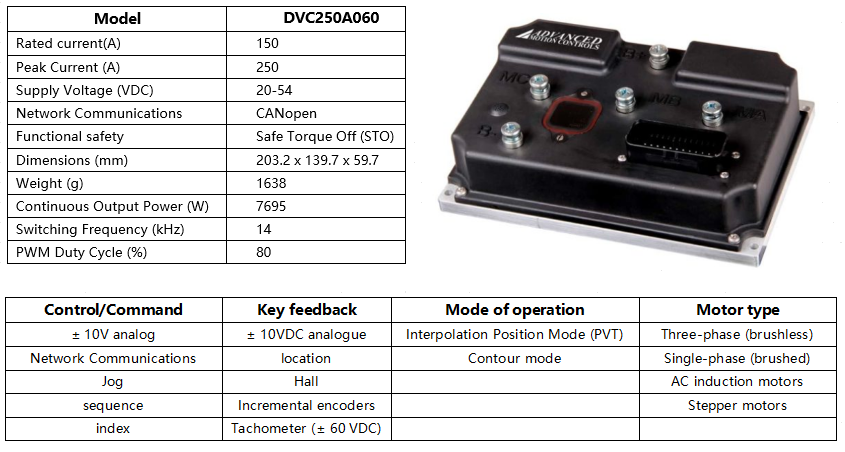
DVC250A060 the panel-mounted servo drive provides full tuning control of all servo circuits and is designed for distributed or centralized server systems. The servo drive uses CANopen@ communication and is debugged with the DriveWare@ via an RS-232 interface
LUGE Steering wheel system MR350LRS - Steering motor drive - DPCANTE-060B080
The MR350LRS Steering motor is equipped with high-end imported brand servo drives, AMC servo drives,
Model DPCANTE-060B080. (If the steering motor uses an absolute code disc motor, the steering motor driver model DPCANTA-020B080 recommended)
Model Parameters

DPCANTE-060B080 Panel-mounted servo driver provides comprehensive tuning control of all servo loops and is designed for distributed
or centralized server systems. The servo drive uses CANopen@ communication and is debugged with DriveWare@ via the RS-232 interface.
LUGE steering wheel system MR350LRS - shunt regulator - LUGE-SR060/080
Features:
★ It is used in low-voltage DC power supply systems
★ Four different clamping voltages are available for user setting
★ The power of the braking resistor can be freely selected
(the current through the shunt circuit needs to be calculated) 
The LUGE-SR series shunt regulators are designed for applications in servo systems where the actuator returns energy during deceleration and causes the bus voltage to rise. During deceleration braking, most of the stored mechanical energy is returned to the power supply, which charges the output capacitor to a higher voltage. If the charge reaches the system overvoltage protection point (controller, amplifier, sensor, etc.), the system will fail. To ensure smooth braking with large inertia loads, a shunt regulator is recommended. Determine the need for a shunt regulator by observing changes in DC bus voltage by braking in the worst case scenario.
The LUGE-SR060/080 allows the user to select four different caliper voltages to meet the needs of the system via a 4-position DIP switch
Logical block diagram
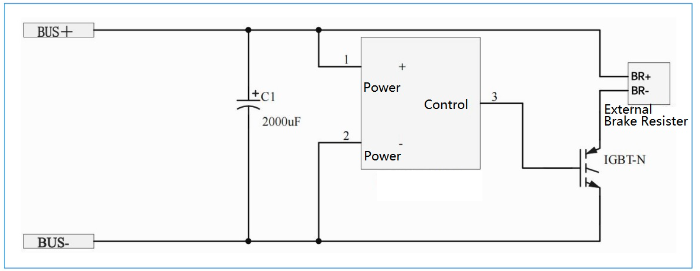
When the DC bus voltage reaches the clamping voltage set by the shunt regulator, the voltage comparator unit turns on the electronic switch
The sub-switch will connect the brake resistor via a DC bus. This power resistor consumes energy from the DC bus. voltage on the bus
When reduced to less than the set clamping voltage, the brake resistor will be disconnected from the DC bus.
LUGE steering wheel system - motor feedback - 2500 line incremental code disc
A 2500-wire incremental disc provides precise position feedback. Optionally, an absolute disc can be mounted directly on the motor shaft (including traction and steering) or on the steering wheel.
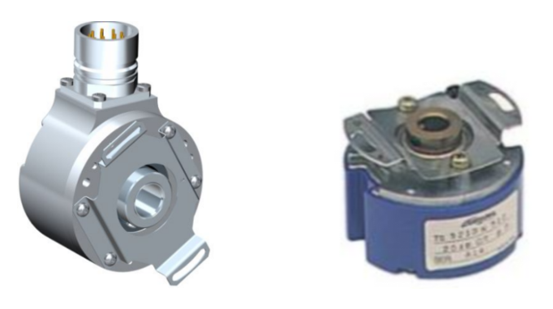
LUGE steering wheel system - cable - high flex cable
It is equipped with a high flexible cable that is resistant to bending and torsion, which greatly improves the working stability and life of the cable. Plug-and-play modular solutions with connectors (energy chain systems, cables, connectors) are available, which greatly increases the ease of installation and maintenance.
The length is determined according to the field wiring design, which is determined by the customer, and the following xx represents x.x0 meters. If you need other cables, please contact our sales engineer.

LUGE steering wheel system (MR350LRS) pre-commissioning and aging treatment
The system configuration of each drive has been completed before leaving the factory, the PID of the tracking motor and the steering servo motor has been pre-debugged and stored in the drive, and all parameters are backed up at the same time, the system has been aging tested, and we provide wiring diagrams, which can greatly save installation and debugging time, and avoid the troubles and systemic risks caused by misoperation, miswiring, parameters and unsmooth debugging.
The debugging file will be sent to the email address specified by the customer by email
Debugging files for travel motor drives:
MR350LRS-TBAKEFILE-DVC250A060+ DRIVE SN NUMBER + CUSTOMER ID
Steering motor drive debugging file:
MR350LRS - SBAKEFILE - DPCANTE-060B080 - Drive SN Number - Customer Identification Code